In flooded chiller systems, it’s common for the condenser to have a higher heat transfer capacity than the evaporator. This difference stems from the physical characteristics of the refrigeration cycle. The condenser is essential for transforming refrigerant from a gas to a liquid state, releasing both the heat absorbed by the evaporator and the additional heat generated during the compression process.
Key Reasons Behind Higher Condenser Heat Transfer
1. Handling Additional Heat from Compression
After the refrigerant absorbs heat from its surroundings in the evaporator, it flows into the compressor, where it's compressed into a high-temperature, high-pressure gas. This compression step adds extra heat to the refrigerant, which the condenser must release. Therefore, the condenser not only dissipates the heat absorbed by the evaporator but also manages the additional heat from compression, resulting in a higher heat transfer demand.2. Enhanced Heat Transfer Area and Design
To accommodate this higher heat load, the condenser typically has a larger heat transfer surface area and an efficient design. These design elements allow it to effectively dissipate more heat and maintain the system's thermal balance, ensuring the chiller operates efficiently across various conditions.3. Ensuring System Stability and Performance
By managing a greater amount of heat transfer than the evaporator, the condenser plays a crucial role in stabilizing the system’s operation. The optimized design and capacity of the condenser allow flooded chillers to meet cooling requirements consistently and with high efficiency, even under variable load conditions.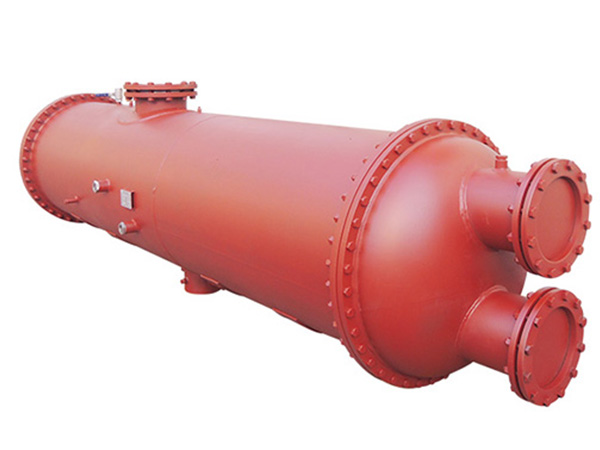
In summary, the condenser's greater heat transfer capacity in flooded chiller systems is due to the combined effects of the refrigeration cycle characteristics and thoughtful system design. This distinction exemplifies the careful application of thermodynamic principles in refrigeration engineering.
评论
发表评论