In the design and operation of data center air conditioning systems, accurately calculating the cooling capacity is a key factor in ensuring efficient and stable operation. This article delves into the methods of calculating cooling capacity and its application in different types of data centers.
1. Methods for Calculating Cooling Capacity
Calculating cooling capacity is the foundation for assessing the air conditioning needs of a data center. The main methods include the power and area methods, taking into account the heat generated by equipment and the environmental heat load.
Formula: Total Cooling Capacity (Qt) = Indoor Equipment Load (Q1) + Environmental Heat Load (Q2)
Q1 = Equipment Power × 1.0
Q2 = 0.12~0.18 kW/m² × Data Center Area
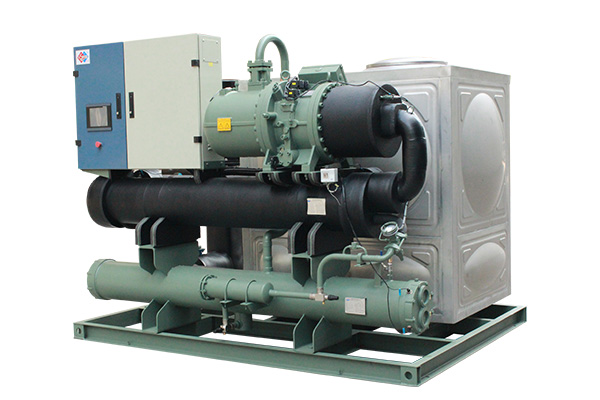
2. Precision Air Conditioning and Cold Load Estimation
For precision air-conditioned spaces such as data centers, cold load estimation needs to consider factors such as equipment heat load, environmental heat load, lighting, and personnel heat dissipation.Estimation Example: For instance, in a 100 square meter room with a total equipment power of 20 kW, wall and ceiling conduction is 5 kW, and window radiation is 2 kW, the total cold load is approximately 27 kW. If the room typically has five personnel, the personnel heat dissipation load is around 500W.
To illustrate how the conduction of building structures affects the cold load of the data center, consider the following example:
Estimation Example: Suppose a data center has the following characteristics:
Walls: Double-layer brick walls with a total thickness of 30cm.
Floor: Concrete, thickness of 10cm.
Ceiling: Gypsum board, thickness of 5cm.
Data Center Area: 100 square meters, height of 3 meters.
The thermal conductivity coefficients (λ) for each material can usually be obtained from building material handbooks. For example, assuming the thermal conductivity coefficient for brick walls is 0.6 W/m·K, concrete is 1.4 W/m·K, and gypsum board is 0.25 W/m·K.
Next, we use the conduction formula Q = U * A * ΔT to calculate the conduction for each section, where:
Q is the conduction (W),
U is the material's thermal transfer coefficient (W/m²·K),
A is the surface area (m²),
ΔT is the indoor-outdoor temperature difference (K).
The calculation formula for U is U = 1 / (d / λ), where d is the material thickness (m), and λ is the thermal conductivity.
By calculating the conduction for each section and summing them up, we can determine the total conduction for the entire data center, thereby estimating the required cold load. This method provides a more accurate way to assess the cooling needs of a data center."
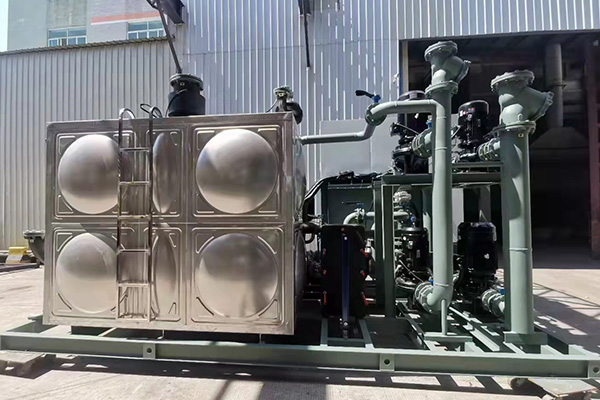
3. UPS Room Air Conditioning Options Calculation
For UPS rooms, the selection of air conditioning involves calculations based on specific heat load conditions, including equipment power consumption, room area, and heat load density.Estimation Example:
Suppose the total equipment power consumption for a UPS room is 50 kW, and the room's area is 100 square meters. Considering a heat load density of 20 W/square meter, assuming the heat load from the area is 100 square meters * 20 W/square meter = 2000 W or 2 kW.
Taking into account both equipment power and the heat load generated by the area, the total heat load is 50 kW + 2 kW = 52 kW. Therefore, an air conditioning system that can provide at least 52 kW of cooling capacity needs to be selected. For redundancy and reliability, additional cooling capacity or an air conditioning system with an N+1 configuration could be considered.
4. IDC Room Air Conditioning Options Calculation
The calculation for selecting air conditioning in IDC (Internet Data Center) rooms is more complex, involving the number of server cabinets, the footprint of each device, and the coefficient of environmental heat load.Q: How to balance redundancy and efficiency in the IDC room air conditioning system?
A: N+1 or higher redundancy configurations can be adopted, while also considering the Energy Efficiency Ratio (EER) or Seasonal Energy Efficiency Ratio (SEER) of the air conditioning system.
Estimation Example:
Assume an IDC room requires a total cooling capacity of 100 kW. To ensure redundancy, an N+1 configuration can be adopted, meaning installing air conditioning units with a total capacity exceeding the required cooling capacity. For example, installing three units, each with a cooling capacity of 40 kW, resulting in a total cooling capacity of 120 kW, with 20 kW as redundancy.
Simultaneously, for efficiency considerations, air conditioning systems with high Energy Efficiency Ratios (EER) or Seasonal Energy Efficiency Ratios (SEER) should be chosen. If the EER for each air conditioner is 3.0, it would consume less energy compared to a system with an EER of 2.5 at the same cooling capacity. This ensures both system reliability (through redundancy) and improves efficiency (by selecting high EER air conditioners).
This approach ensures that the IDC room's air conditioning system can maintain normal operation even if one unit fails and optimizes energy efficiency under normal operating conditions.
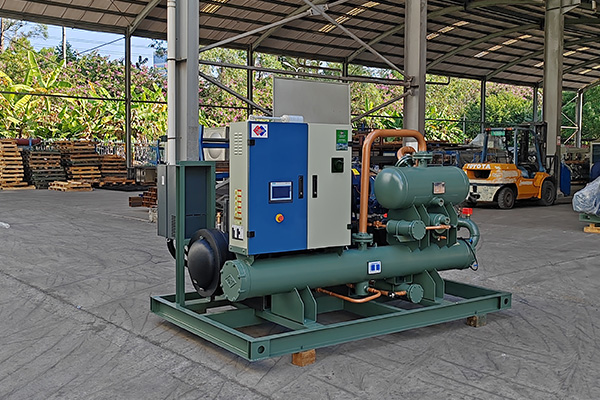
5. Cleanroom Air Conditioning Load Calculation for Manufacturing Workshop
When calculating the air conditioning load for a manufacturing workshop, various factors need to be considered, including the heat generated by equipment, heat from personnel, lighting, external environmental heat load, and the required air cleanliness in the workshop. Here's a specific calculation example:Estimation Example:
Assume a manufacturing workshop has an area of 200 square meters and a height of 3 meters. The workshop has heat-generating equipment with a total power of 30 kW. On average, there are 10 workers in the workshop, each generating approximately 100W of heat. The total power of the workshop's lighting equipment is 5 kW. Assuming an external environmental heat load of 10 kW and an additional 5 kW load for maintaining air cleanliness, the total heat load is calculated as follows:
Equipment heat load: 30 kW
Personnel heat load: 10 people × 100W/person = 1 kW
Lighting heat load: 5 kW
External environmental heat load: 10 kW
Air cleanliness maintenance: 5 kW
Total heat load = 30 kW + 1 kW + 5 kW + 10 kW + 5 kW = 51 kW
Therefore, the manufacturing workshop requires an air conditioning system with a minimum cooling capacity of 51 kW. Depending on actual needs, it might be necessary to consider some redundancy to ensure a suitable working environment during high load periods or equipment failures.
评论
发表评论