1、 Introduction:
With the implementation of the national strategy of developing the ocean, the use of petrochemical devices on my country's offshore platforms has developed rapidly. Seawater heat exchanger is an important equipment that is most widely used in offshore platform operations. The heat exchange status of the heat exchanger directly affects the smooth operation of the entire platform and the comprehensive economic indicators, and has a great impact on the safety, stability and long-term operation of production. It plays an important role.
The selection of materials is a very important link in the design of seawater heat exchangers. Whether the selection of materials is appropriate has a great impact on the production, safety, maintenance and technical transformation of the device. For the selection of heat exchanger materials, the relevant standards and specifications should be strictly followed, and the best materials should be selected according to the mechanical properties of materials, chemical composition, manufacturing process conditions and the actual situation of the owner. It is of great practical value to master the essentials of material selection methods and understand the process of correct material selection. In this paper, in the marine environment, the matters needing attention in the selection of seawater heat exchanger materials are sorted out and analyzed, and reasonable suggestions are put forward.
2、 The main factors affecting the selection of seawater heat exchanger materials
1) Medium characteristics
The performance of the medium includes the corrosiveness of the medium, temperature, pressure, flow rate, etc., which will greatly affect the selection of materials. According to different actual working conditions, it should be the primary consideration for material selection.
As one of the medium of seawater heat exchanger, seawater has a high content of dissolved oxygen, chloride ions and microorganisms, which is highly corrosive to seawater heat exchangers; at the same time, the corrosive properties of another medium for heat exchange should also be considered. , such as inorganic salts, sulfides, nitrides, organic acids, etc. contained in crude oil, and natural gas contains hydrogen sulfide, sulfur dioxide, hydrogen, etc. The velocity of the fluid medium will produce erosion, abrasion, etc., especially when the fluid contains solid particles. The working temperature seriously affects the performance of the material. When the temperature increases, the strength of the material decreases, and even creep occurs, resulting in direct failure of the material; when the temperature decreases, the ductility and toughness of the material will also decrease. If the temperature is lower than the cold-brittle transition temperature, the material will also fail.
2) The performance of the material
The marine environment is a specific and complex environment with harsh climatic conditions. In the atmosphere of this area, water vapor, oxygen, nitrogen, carbon dioxide, sulfur dioxide, and chloride salts, sulfates, etc. It has obvious characteristics such as high humidity, high salinity, high temperature and dry and wet cycle effects.
The performance of the material is mainly based on the working environment, mechanical load conditions, and the corresponding material is selected according to the performance index of the material. According to the special working environment of the offshore platform, considering the heat exchanger performance requirements of the seawater heat exchanger, the performance that the heat exchanger material should meet mainly includes high thermal conductivity and sufficient mechanical strength.
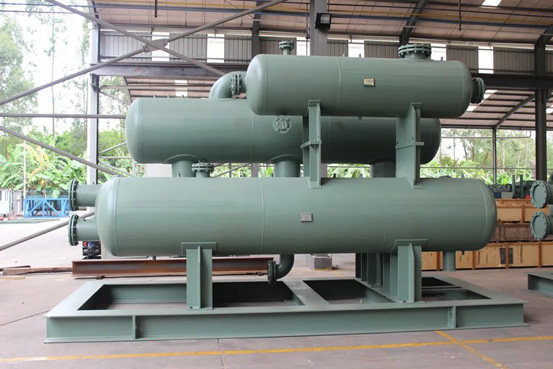
3) Processing properties of materials
The machinability of materials refers to the difficulty of using different processing techniques, different processing equipment and various welding techniques to manufacture products, which is also a factor that must be considered in the actual production process of the equipment. The ideal heat exchanger material should not only meet sufficient performance, but also have excellent casting performance, machining performance, pressure processing performance and heat treatment process performance. At the same time, the processing performance of the material and the welding process performance should also be considered. For example, the processing performance of titanium materials is poor, low carbon steel is easier to weld than high carbon steel, and stainless steel requires special welding processes. These should be fully considered when selecting materials.
4) Cost
Cost accounting should be carried out when selecting materials, and the most cost-effective materials should be selected by fully considering the cost of the material itself, the cost of processing technology, and the cost of transportation. The best material selection has the lowest cost life For example: sometimes it is more economical to use carbon steel with increased corrosion allowance than to use more expensive corrosion resistant materials (refer to the sum of material cost and manufacturing cost). When stainless steel and other precious alloy materials must be used, if the thickness is relatively thick, carbon steel or low alloy steel can be used as the base layer of composite steel plate or metal lining, which is more economical; in some corrosive occasions, corrosion-resistant materials can be used As a lining or coating.
5) Weight
Generally, equipment that is fixed on land is less concerned with weight restrictions, but if it is placed on an offshore oil platform, ship, etc., the weight of the equipment is also an important factor affecting the selection of materials. Offshore platforms seawater heat exchangers should fully consider the transportation costs and installation costs of transporting them to the platform.
For more details ,welcome to contact us for more at https://www.hstarschiller.com
评论
发表评论