Shell and tube heat exchanger is a kind of heat transfer device, which is composed of shell, tube plate, tube bundle, baffle and cover; How is the manufacture to produce the shell and tube heat exchanger?
In the manufacturing of heat exchanger, the manufacturing process of cylinder, head and other parts is the same as that of general container manufacturing progress, but the requirements are different. The inspection of materials, drilling of tube plate and baffle hole, welding of cylinder and processing of flange are the key points to the quality. Throughout its manufacturing process, most of manufacturer still use traditional processes, in which the proportion of welding is relatively high, so it is necessary to weld in strict accordance with the welding process, and to detect the weld. The heat exchanger produced by H.Stars Group subsidiary company UAR, has gone through 18 processes. It has been meticulously processed in the heat exchanger process, providing two products with guaranteed quality and maximum heat exchange efficiency for the water chiller, and providing customers with a satisfactory answer sheet.
Looking around the world, in the past, the precision technology of heat exchanger was often in the hands of developed countries in Europe and the United States, but after continuous development, learning and absorption, H.Stars Group subsidiary company UAR has made remarkable achievements in the field of heat exchanger. Before and after the introduction of advanced CNC machine tools from Taiwan and abroad, absorbing advanced processing technology from abroad and at the same time, they also strive to innovate, heat exchanger products to process design science Reasonable, keep improving, provide competitive price and high quality products for the market.
The heat exchanger is also the most important part of the four parts for the whole chiller. Its quality affects the service life and maintenance cost of the whole chiller. Below is the key production process of the H.Stars subsidiary company UAR high standard heat exchanger
I. Design
The company has special equipment pressure vessel design, manufacturing qualification and R & D team. The heat exchange capacity of each heat exchanger is reasonably calculated and selected by relevant software.
II. Incoming material inspection
The materials used for heat exchanger (steel plate, steel pipe, heat exchange pipe and nozzle accessories) are purchased in strict accordance with national and industrial standards, and the corresponding original quality certificate is provided. After the arrival of the materials, the quality inspection department shall go through the warehousing procedures after they pass the inspection.
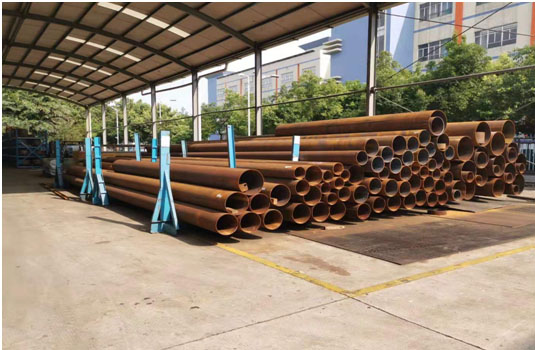
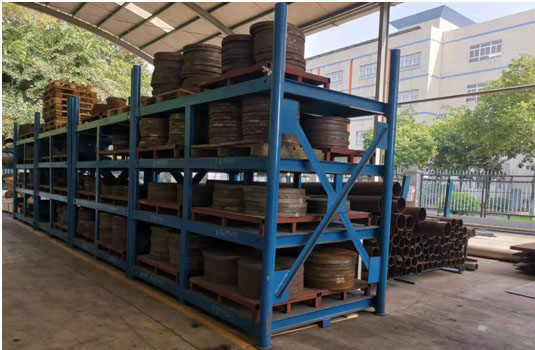
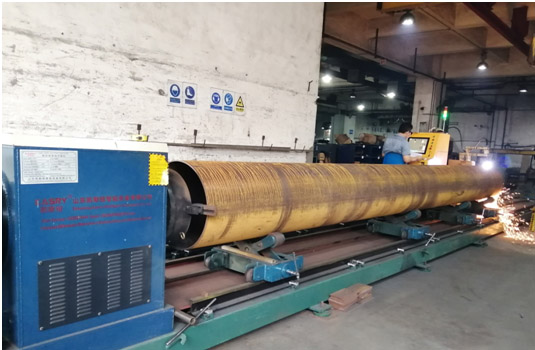
1. Heat exchanger cutting: CNC cutting machine, CNC pipeline cutting machine and CNC plate cutting machine are used. After the steel plate and steel pipe are cut off, the identification shall be transplanted, and the material shall be cleaned on the pickling surface to make the cleanliness of the heat exchanger up to the standard.
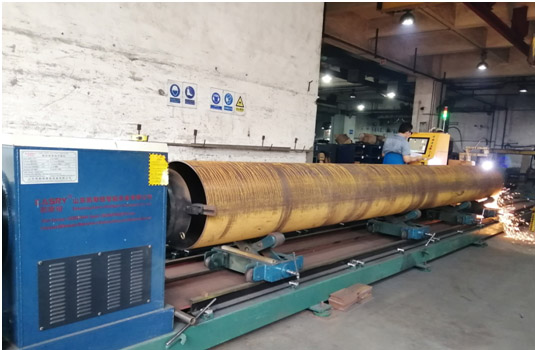
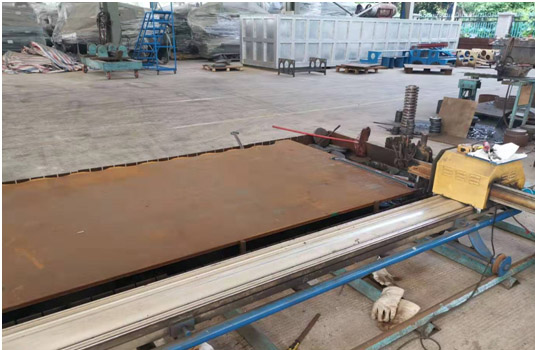
2. Rolling & barrels making : large heat exchanger is rolled by numerical control rolling machine and welded by submerged arc automatic welding machine. Class II of 100% RT for class A and B welds is acceptable.
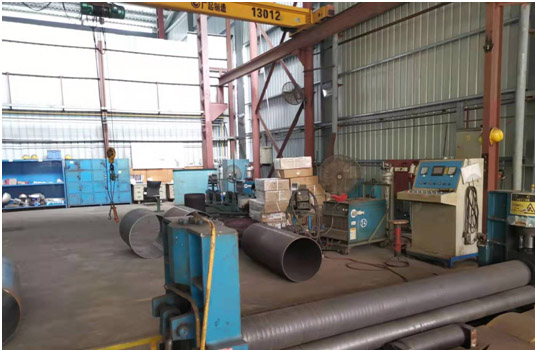
3. Pickling: steel plate and steel pipe after pickling and phosphate are stored for a longer time than those after sandblasting and shot peening, which is not easy to return to rust. Meet the product cleanliness control requirements in the manufacturing cycle.
In the manufacturing of heat exchanger, the manufacturing process of cylinder, head and other parts is the same as that of general container manufacturing progress, but the requirements are different. The inspection of materials, drilling of tube plate and baffle hole, welding of cylinder and processing of flange are the key points to the quality. Throughout its manufacturing process, most of manufacturer still use traditional processes, in which the proportion of welding is relatively high, so it is necessary to weld in strict accordance with the welding process, and to detect the weld. The heat exchanger produced by H.Stars Group subsidiary company UAR, has gone through 18 processes. It has been meticulously processed in the heat exchanger process, providing two products with guaranteed quality and maximum heat exchange efficiency for the water chiller, and providing customers with a satisfactory answer sheet.
Looking around the world, in the past, the precision technology of heat exchanger was often in the hands of developed countries in Europe and the United States, but after continuous development, learning and absorption, H.Stars Group subsidiary company UAR has made remarkable achievements in the field of heat exchanger. Before and after the introduction of advanced CNC machine tools from Taiwan and abroad, absorbing advanced processing technology from abroad and at the same time, they also strive to innovate, heat exchanger products to process design science Reasonable, keep improving, provide competitive price and high quality products for the market.
The heat exchanger is also the most important part of the four parts for the whole chiller. Its quality affects the service life and maintenance cost of the whole chiller. Below is the key production process of the H.Stars subsidiary company UAR high standard heat exchanger
I. Design
The company has special equipment pressure vessel design, manufacturing qualification and R & D team. The heat exchange capacity of each heat exchanger is reasonably calculated and selected by relevant software.
II. Incoming material inspection
The materials used for heat exchanger (steel plate, steel pipe, heat exchange pipe and nozzle accessories) are purchased in strict accordance with national and industrial standards, and the corresponding original quality certificate is provided. After the arrival of the materials, the quality inspection department shall go through the warehousing procedures after they pass the inspection.
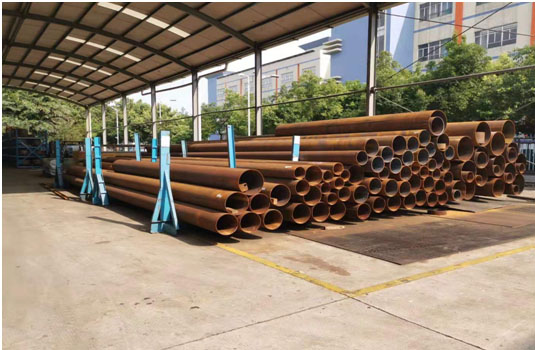
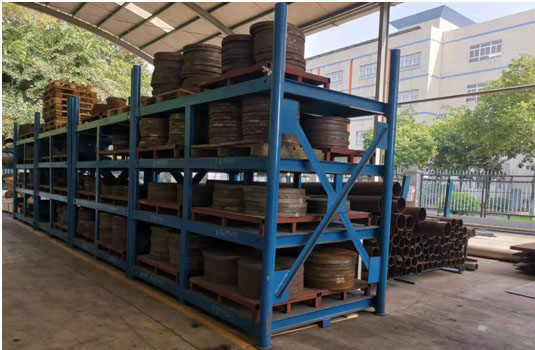
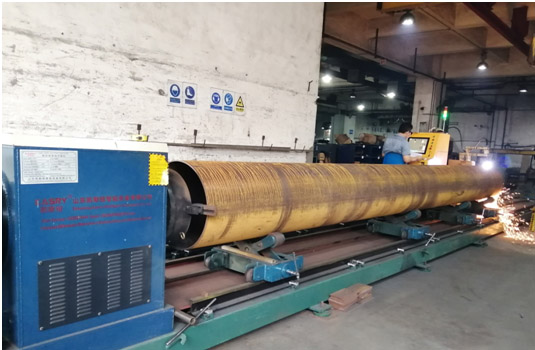
1. Heat exchanger cutting: CNC cutting machine, CNC pipeline cutting machine and CNC plate cutting machine are used. After the steel plate and steel pipe are cut off, the identification shall be transplanted, and the material shall be cleaned on the pickling surface to make the cleanliness of the heat exchanger up to the standard.
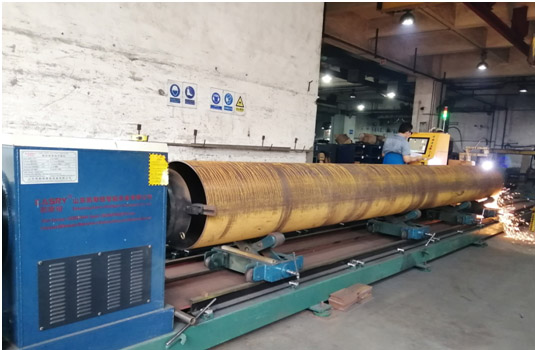
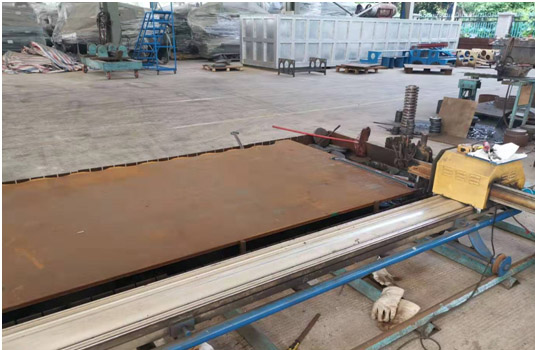
2. Rolling & barrels making : large heat exchanger is rolled by numerical control rolling machine and welded by submerged arc automatic welding machine. Class II of 100% RT for class A and B welds is acceptable.
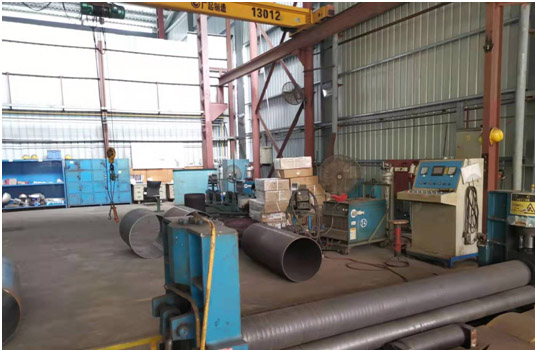
3. Pickling: steel plate and steel pipe after pickling and phosphate are stored for a longer time than those after sandblasting and shot peening, which is not easy to return to rust. Meet the product cleanliness control requirements in the manufacturing cycle.
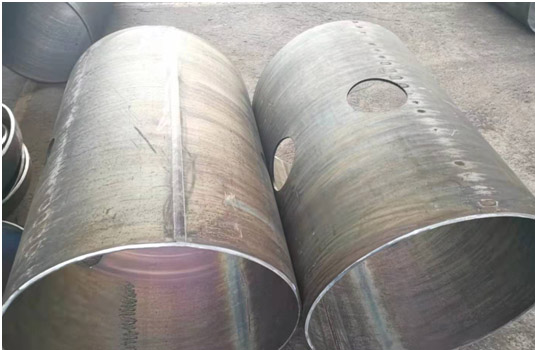
评论
发表评论